In this article:
- Movingfluid systems: top-class performance and camouflage capability
- Driving the future with Nikola and IVECO
- From software to mechanics, the challenge: precision and customisation at the highest levels
- A job without challenges is not for us!
- The solution: time schedule observed in every detail
- Fast forward to a new partnership
Movingfluid systems: top-class performance and camouflage capability
The case history we are going to tell you about involves the realisation of completely customised fluid dispensing systems alongside Nikola and IVECO, with reference to the revolutionary project stemming from their partnership. Announced at the end of 2019, and still in the news in the most important magazines in the sector, and not only, the step taken by the two companies is destined to mark the future of electric mobility forever. The result of this commercial synergy is Nikola Tre, the electric truck with a stylish and attractive design that is already in great demand on the market.
The ability of Movingfluid to work on totally customised orders and to integrate its own creations in a mimetic manner into existing industrial plants meant that, once again, legendary brands from the automotive sector selected our team to support them with ingenious solutions in an important project.
More specifically, the challenge taken on by Movingfluid that we are about to share with you is aimed at designing and creating dispensing systems to transfer the necessary fluids inside the engine and other parts of the vehicle, thus preparing the vehicle for the road.
Not least, the dispensers must perfectly reflect the look and feel of the production environment, matching the aesthetics of the existing machinery.
As was the case with Lamborghini, for whom we created ad hoc paint booths for the finishing of luxury cars, our expertise in fluid handling is now being tested for inclusion in the process of preparing the brand-new electric vehicle.
Wherever it is a must for systems to meet stringent performance requirements and aesthetics, Movingfluid is unrivalled. Are there only a few units to be produced? Should the suppliers be those already chosen by the company? Do the devices have to fit into an existing production line, comply with certain measures and be accompanied by user manuals drawn up according to company standards?
To all these requests we are prepared to say yes.
Are you ready to put your foot on the accelerator and test the first Nikola Tre electric trucks with us?
Driving the future with Nikola and IVECO
After announcing a series of zero-emission vehicle concepts in 2016, the Nikola Corporation has now moved into action, taking the lead in the production of clean energy vehicles themselves.
As large diesel trucks have a high carbon footprint (one diesel semi-trailer emits as much carbon as 14 petrol cars), converting heavy vehicles to zero-emission vehicles is certainly a prime objective in terms of environmental benefit.
With the inauguration of the German plant in Ulm intended for the final assembly of electric vehicles, the newly founded company Nikola IVECO Europe GmbH is moving swiftly towards the mass production of Nikola Corporation trucks and designed on the basis of the Italian company’s S-Way.
And it is precisely at the Ulm production site that our mishap-solvers are called upon to intervene with a brilliant solution, contributing with their know-how to the creation of a fluid dispensing system in line with the very high-quality standards required.
We can only be honoured for the responsibility that has been bestowed upon us and happy to have contributed with a small but crucial piece of this important transport development. Positioned as the last step on the assembly line, the fluid dispensing system actually provides the truck with the vital energy it needs to start, before the vehicle is finally put on the road.
A road that we hope will be long not only in terms of kilometres travelled, but also in terms of goals achieved, opening the door to an increasingly green future of mobility.
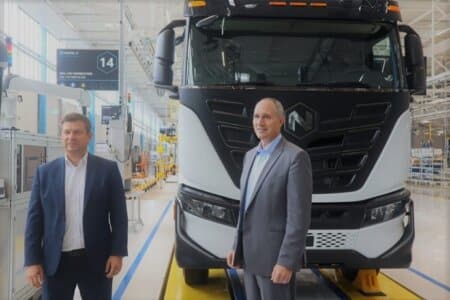
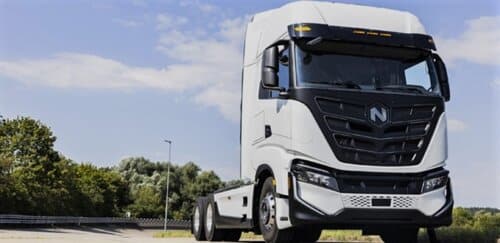
From software to mechanics, the challenge: precision and customisation at the highest levels
In August 2020 Nikola IVECO Europe GmbH launches a tender for the creation of four fluid dispensing systems to be installed on the new assembly line at Nikola‘s new plant in ULM.
The machinery in question is designed to dispense the following fluids in succession on the vehicle preparation line before the vehicle is put into service:
- power steering oil for braking system
- Paraflù radiator fluid (two different types of product)
- filling for gas R134A for air conditioning circuit
- windscreen washer fluid DP1
A turnkey design is required for systems that are easy to move and that have:
- state-of-the-art HMI (Human Machine Interface) software in German and English;
- integration for all four systems with centralised local supervision software capable of identifying individual machines and monitoring their behaviour and performance, including error logging;
- production control with a C3 approach (Communication, Command, Control), capable of monitoring and recording the operation of each individual plant (quantity dispensed, vacuum pressure, etc.), making the information available for any data recovery needs;
- production chain traceability: process data exchange at MES (Manufacturing Execution System) level 3, through a complete and dynamic software system capable of monitoring, tracking, documenting and controlling the production process, providing decision-makers with the necessary elements to make process improvements.
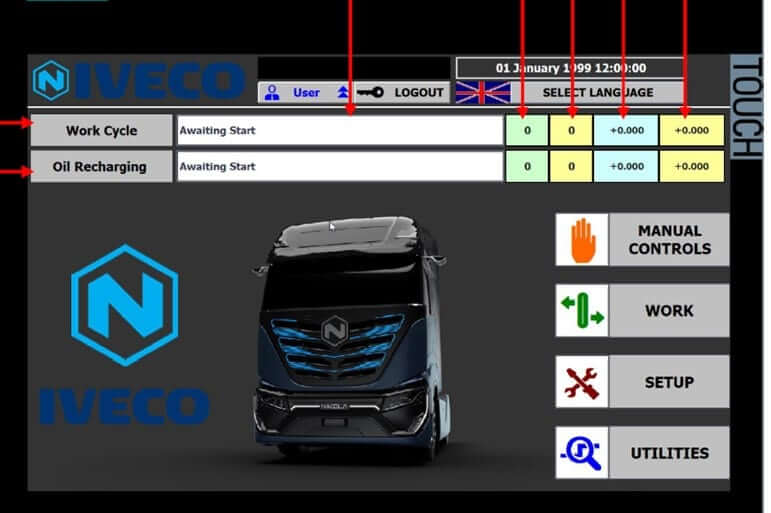
A job without challenges is not for us!
There were plenty of difficulties for our mishap-solvers to overcome. The design and manufacture of the four dispensers required a radical re-engineering of the aesthetic and functional parts, including:
- fully customised software: the image above shows the graphical interface of the programme we supplied;
- procurement of commercial components restricted to company guidelines in terms of product codes and suppliers, so as to achieve perfect visual alignment with the existing system.
As far as the structural parts of the pumping system are concerned, Movingfluid offered its added value in the selection of the best performing items, thanks to its in-depth and up-to-date knowledge of the solutions available on the fluid handling market; - very short delivery times: the installation of the machines, including final testing, is requested no later than six calendar months from the order date. The deadline is imperative, dictated by the delivery commitments already made by the company to its customers. Deliveries of Nikola Tre are scheduled to begin by 2022 for the first selected lucky buyers in the United States.
Do you want a unique fluid dispensing system branded with your name?
The solution: time schedule observed in every detail
How can such a complex, highly specific and urgent project be tackled effectively without meticulous planning from the outset?
Does that seem trivial? Precision is at home here. We consider this to be a form of respect towards the customer: we always keep our commitment without delay and without excuses, as unfortunately often happens.
Using Gantt charts, we then created and shared a map of the total project with the customer, including activities, roles, delivery schedules and technical interventions for the installation of the machinery.
After an initial phase of careful design by our technical office specialising in fluid engineering, we quickly moved onto implementation.
Coordinating with the customer on a continuous basis, several times a week, we developed the project in parallel for all supply sections, arriving at delivery and testing of the filling systems on the planned date in relation to the schedule compiled six months earlier.
A great deal of teamwork enabled us to meet Nikola IVECO Europe‘s requirements in terms of function and aesthetics, making it possible to use the fluid dispensers to get the new battery-powered truck on the road without any production delays.
The system also has a level of precision that reduces waste to a minimum, below 0.3%, allowing optimum use of the substances used (oils, gases, liquids) and virtually eliminating the need for any maintenance work.
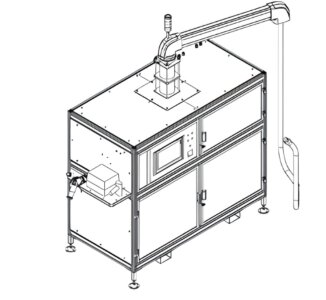
Fast forward to a new partnership
The four fluid dispensing systems were installed and tested not only on schedule, but also in accordance with the WMC (World Class Manufacturing) procedures that the Ulm site operates under. This acronym refers to an innovation programme based on continuous improvement and the systematic reduction of production costs by eliminating all types of waste. Zero waste, zero accidents, zero breakdowns and zero stock. This can only be achieved through the use of rigorous methods, objective measurements and the involvement of everyone.
Compliance with this methodology now qualifies the world’s leading manufacturers of goods and services and is widely used in the automotive sector.
An example of an application stemming from this philosophy is the commitment by the supplier to guarantee autonomy to the end user of the asset in case of need for future maintenance or interventions, by providing a detailed and exhaustive instruction manual, covering every case.
We have met this demand by providing multilingual analyses and documents, aligning our supply with the customer’s standard technical manuals.
As a result of customer satisfaction, IVECO awarded us another order to supply the Brescia plant. The same fluid dispensing system is ready to be used on Daily 4x4s, …but we’ll talk about this in an upcoming article!
Continue reading our Journal!
If, on the other hand, you want to test us with a system, the most difficult one you can imagine
- Alstom [1]
- ARO Ingersoll Rand [1]
- Automotive [8]
- Brembo [2]
- Case History [13]
- Cast iron brakes [1]
- Ceramic [2]
- Chemical [3]
- chemical mixer [1]
- Chemistry [2]
- Cleaning [1]
- cleaning industrial machinery [1]
- Dilution [1]
- Dosage [4]
- Dust [1]
- Extrusion [3]
- Finishing [1]
- Fluid handling [3]
- Fluids [2]
- Food [1]
- Freni in ghisa [1]
- Gases [3]
- Glue [2]
- Henkel [1]
- Industrial Painting [4]
- IVECO [1]
- Know-how [2]
- Körber Tissue [2]
- Lamborghini [2]
- Liquid paint [1]
- Liquids [6]
- LPR [1]
- Market news [4]
- mixing chemicals [1]
- Nikola [1]
- Oenology [2]
- Oil & Gas [1]
- Paint [2]
- Paper [2]
- Paper converting [1]
- Paper industry [2]
- Powder Coating [1]
- Powders [1]
- pump test bench [1]
- Raw material producer [1]
- Saipem [1]
- Spraying [5]
- Streparava [1]
- SuperSix [1]
- Tissue [3]
- Tissue converting [2]
- Toscotec [1]
- Trail [1]
- Transfer [7]
- Verniciatura industriale [3]