In this article:
- IR+ADIA technology conquers all sectors
- Powder coating on metal: how it works
- IR+ADIA on powder-coated metal: a new challenge for our “mishap-solvers”
- The test: IR+ADIA on powder-coated metal
- Test results: early and good … pays off!
- Conclusion: IR+ADIA advantages in powder coating baking on metal
- IR+ADIA: the future is certain, also in contract coating
IR+ADIA technology conquers all sectors
Test after test, customer after customer, IR+ADIA technology is making inroads into all applications and sectors to date due to its ability to drastically reduce coating baking times while ensuring high quality levels.
After analysing the success of liquid coating on plastics, in this article we will see how even powder-coated metal surfaces can achieve perfect curing in the shortest possible time and space using IR+ADIA technology.
For many industries, this solution may prove to be a breakthrough that optimises processes and the use of space within the plant, but for those specifically involved in contract painting, it may even be the salvation of their business. IR+ADIA technology applied to powder-coated metal makes it possible to speed up production and increase production capacity without affecting the quality and strength of the finished product. We will go into this in more detail below.
For the moment, please follow us in this test that has seen Movingfluid technicians, professionals in fluid handling, working alongside a brand leader in the production of industrial machines for use in various fields.
The challenge for us “mishap-solvers” was to achieve perfect quality coating results, even on very large sheet metal surfaces, much faster than in the past. To guarantee a result making them so satisfied that they would have no hesitation in making the final choice, with numbers and laboratory analyses to back it up.
To identify, in short, a technology that could justify a radical and committed change in their approach to painting.
Below is how it went.
If you don’t want to be the last to experience the benefits of IR+ADIA,
book your paint process test now.
Powder coating on metal: how it works
The benefits offered by the powder coating process are diverse and of fundamental value within the scope of applications to metal surfaces, such as steel and aluminium. As well as protecting against corrosion, powder-coated metal also has excellent thermal and electrical insulation properties.
Understanding the process normally used for powder coating is a prerequisite for realising the advantage generated by the brilliant solution by Movingfluid described below.
The main characteristic of powder coating is the lack of solvent within the composition itself. The dye is composed of organic materials including resins, pigments and any additives, ground into very small particle sizes of between 20 and 120 millionths of a metre. This is referred to as micronized powder.
Two types of paint can be used:
- thermosetting powder coatings: these are the most commonly used. They offer good protection against corrosion and chemical aggression;
- thermoplastic powder coatings: these coatings do not liquefy with heat and cooling does not cause changes to their original chemical composition. This type of coating is preferred when a higher degree of protection is required.
Painting is carried out dry and the adhesion of the powder to the surface to be treated is achieved through the use of a catalyst, i.e. a tool that combines air and powder through the electrostatic phenomenon. Powder coating is thus subjected to a negative charge, while the metal material to which it is to be applied is grounded.
The powder-coated metal is then placed in a special baking furnace at a temperature close to 180°C. Here, the powder first melts and then polymerises, covering the object with a thin but durable and homogeneous layer of varnish.
The polymerisation process using a conventional paint furnace takes about 20 to 30 minutes.
How can such long waiting times be reduced and the next steps be taken more quickly, without affecting quality in terms of strength and appearance?
IR+ADIA on powder-coated metal: a new challenge for our “mishap-solvers”
Below is the starting situation, i.e. the steps and times required for baking the painted metal surfaces with a thermal convection furnace, based on the traditional process implemented by the client company:
- application of the neutral primer
- first firing of the neutral primer: 5 – 10 min.
- waiting for neutral primer to dry
- application of coloured paint
- second baking at 180°C in the furnace: 15 – 20 min.
- cooling of the part: 10 min.
Estimated total cycle time: approx. 40 – 50 min.
By aiming to reduce the production cycle time through the use of IR+ADIA, Movingfluid simultaneously aims to solve two problems related to the procedure described above:
- large paint baking furnaces, which are necessary to properly polymerise the powder deposited on the items;
- large spaces are required to perform the entire cycle: the application of a primer and finishing powder implies double firing cycles which further increase the length of the furnaces and post-firing cooling lines.
We like to call ourselves “mishap-solvers” because we have a special eye for spotting problems, even minor or related ones, and turning them into strengths. We offer solutions which, when applied to industrial processes and plants, bring advantages in every respect: operational, economic, qualitative and aesthetic. We have talked here about what we could do just for you!
A “jinx” with your trial?
The test: IR+ADIA on powder-coated metal
Paints used in the test stage:
In compliance with our client’s internal guidelines, they were used for testing:
- Sherwin-Williams powder primer, code 46382 MP BT HI EDGE PRIMER ESD GREY
- Sherwin-Williams powder enamel green, SW code 58616 PE/P TB BT LT VE CH. IMER 09
Other powder coatings can be used as an alternative: the benefits of IR+ADIA technology are to be quantified on a case-by-case and application-specific basis.
Procedure followed for the test
- application of powder primer;
- primer gelling with IR lamps: this treatment, as an alternative to baking and drying the paint, makes it possible to completely eliminate a very long work phase.
The best result was achieved by exposing the part painted with primer to 1 minute of radiation.
- immediate application on the surface of the enamel powder (finishing powder)
- final firing and cross-linking using IR lamps
- cooling with adiabatic system
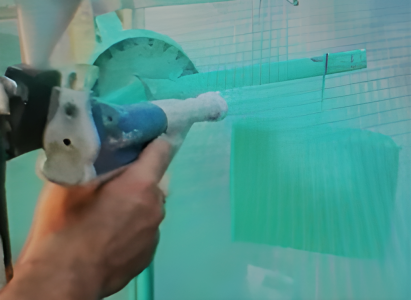
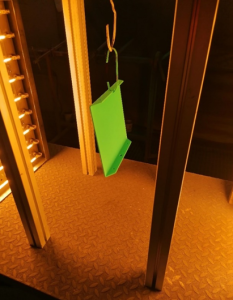
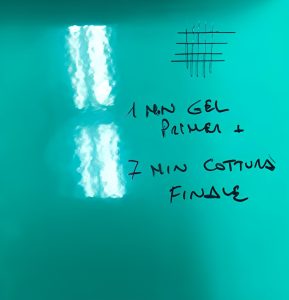
Test results: early and good … pays off!
Reducing production cycle time
This table compares the times of the standard production process, with hot air furnace, and those of the new cycle with IR+ADIA (paint baking in IR furnace + adiabatic cooling).
The data collected left no doubt: treatment with IR+ADIA was unquestionably faster and more cost-effective.
Paint polymerisation with IR+ADIA technology | Paint polymerisation with conventional furnaces | Time saved using IR+ADIA technology | % of improvement (production increase) | |
Primer gelling time | 1 minutes | 5-10 minutes primer firing | 4-9 minutes | 75%-90% |
Primer cooling | NOT REQUIRED | 10 minutes | 10 minutes | 100% |
Final colour polymerisation time | 7 minutes | 15-20 minutes | 8-13 minutes | 48%-62% |
Cooling time | 5 minutes | 10 minutes | 5 minutes | 50% |
Cycle time tot. | 13 minutes | 40-50 minutes | 27-37 minutes | 66%-78% |
IR+ADIA treatment resistance: salt spray test
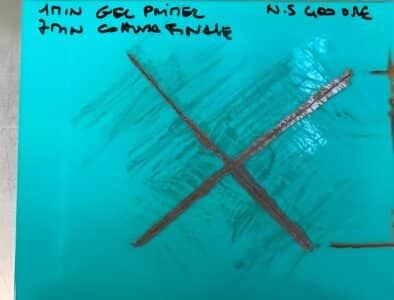
The parts painted during the tests were subjected to a 400-hour salt spray test to check their quality and resistance.
The test showed a very good final result with a final penetration along the cross of max. 3 mm on each side of the engraving.
This result confirms:
- effectiveness of IR+ADIA technology for fast drying powder coating on metal surfaces;
- IR+ADIA allows you to apply the second coat on top of the gelled primer without having to wait for it to dry completely.
Conclusion: IR+ADIA advantages in powder coating baking on metal
The test described above shows how the IR+ADIA paint drying system applied to painted metal surfaces can turn the initial problems into strengths:
- reduced production time: more can be produced in the same space for the same amount of time;
- reduction of space needed in the production cycle: producing the same quantities requires less space than a traditional system;
- reduced energy consumption: IR+ADIA technology allows energy to be consumed only and exclusively when the workpiece to be irradiated is present, with no need for pre-heating or energy loss to maintain temperatures. Energy can be made available by simply switching ON/OFF the control commands, thereby allowing for a reduction of CO2 emissions into the atmosphere.
Are you already familiar with the Movingfluid method?
In fluid handling, many people talk about us.
Our assistance goes well beyond ordinary support.
IR+ADIA: the future is certain, also in contract coating
There are many industries for which metal powder coating is an integral part of the production cycle. To name a few:
- Agricultural Contraction Equipment: painting of agricultural and construction machinery
- household appliances: painting of small and large appliances
- architecture: painting of architectural elements such as facades, windows and doors
- automotive: vehicle painting and repair
- general industry: painting of elements such as valves and fittings for water and gas installations
- furniture: varnishing of furniture and accessories, especially on MDF panels
- lighting, electronics, electrical engineering: painting of electronic components, ceiling lights,..
Powder coatings are also widely used by companies that specifically deal with contract painting. Highly professional companies operating in a wide range of sectors, intervening at different levels in the production and assembly chain of a very large number of articles.
And yet it is precisely for this category, exhausted by years of economic and commercial strategies based on low prices, that the fall in profit margins seems to have no other outcome than exasperated productivity, with an increase in hours worked at the expense of ever-lower quality.
The lack of a guaranteed result is pushing many brands to “bring in-house” the painting phase, thus avoiding any risk associated with the provision of this service by a third party, hanging on to deliveries with increasingly uncertain quality yields and delivery times.
So, the advantages of IR+ADIA come as a gift with immense potential for contract painters:
- reduced time, higher productivity for the same number of hours worked, resulting in higher profits;
- less space occupied and versatility in handling different jobs or different colours even simultaneously;
- a high level of quality to satisfy even the most demanding and responsible customer, who is careful to evaluate the technical, economic and environmental performance of what they buy.
Painters are free to return to their professionalism and to find satisfaction in their work and the certainty of a solid future.
Are you a contract painter?
Show that you are ahead.
Attract smart customers.
- Alstom [1]
- ARO Ingersoll Rand [1]
- Automotive [8]
- Brembo [2]
- Case History [13]
- Cast iron brakes [1]
- Ceramic [2]
- Chemical [3]
- Chemistry [2]
- Cleaning [1]
- Dilution [1]
- Dosage [4]
- Dust [1]
- Extrusion [3]
- Finishing [1]
- Fluid handling [1]
- Fluids [2]
- Food [1]
- Freni in ghisa [1]
- Gases [3]
- Glue [2]
- Henkel [1]
- Industrial Painting [4]
- IVECO [1]
- Know-how [2]
- Körber Tissue [2]
- Lamborghini [2]
- Liquid paint [1]
- Liquids [6]
- LPR [1]
- Market news [4]
- Nikola [1]
- Oenology [2]
- Paint [2]
- Paper [2]
- Paper converting [1]
- Paper industry [2]
- Powder Coating [1]
- Powders [1]
- Raw material producer [1]
- Spraying [5]
- Streparava [1]
- Tissue [3]
- Tissue converting [1]
- Toscotec [1]
- Trail [1]
- Transfer [7]
- Verniciatura industriale [3]